What Is Used To Repair Big Brass Band Instruments
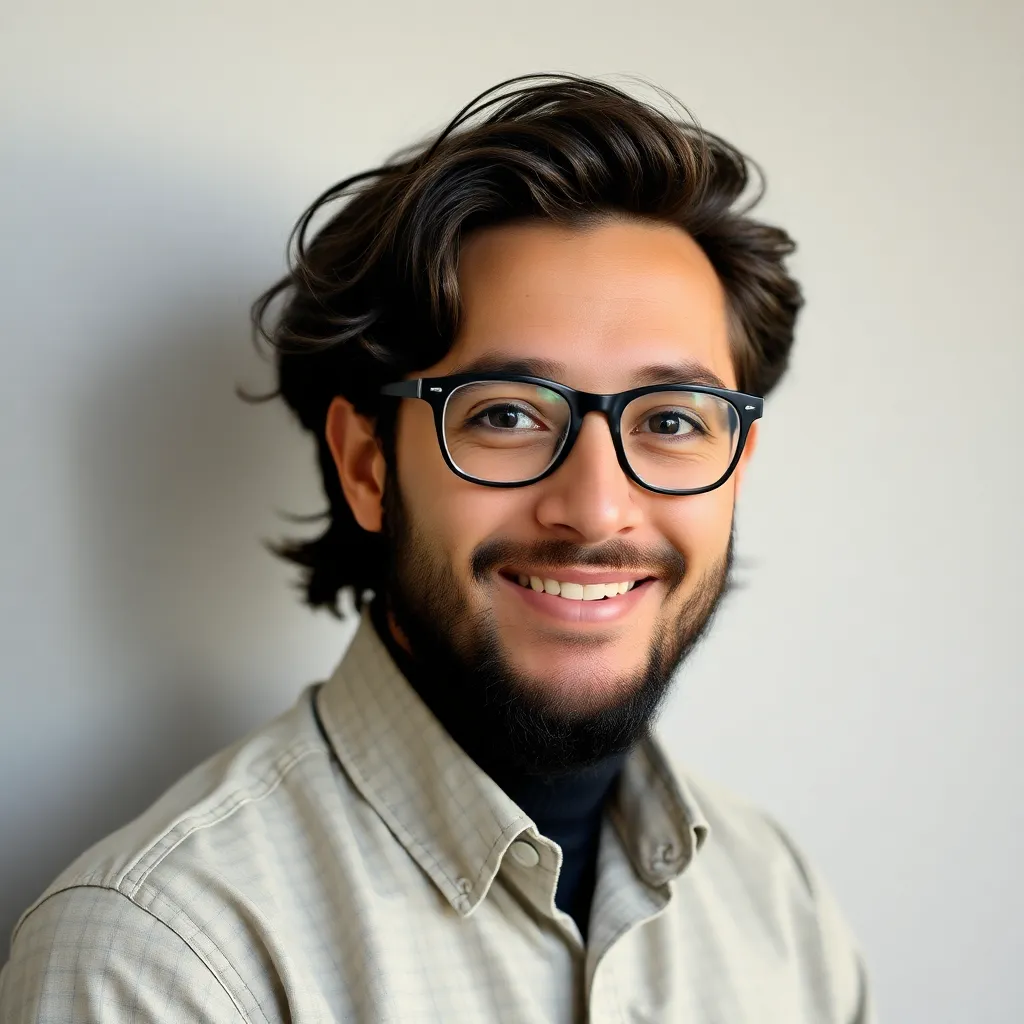
Arias News
Apr 08, 2025 · 5 min read
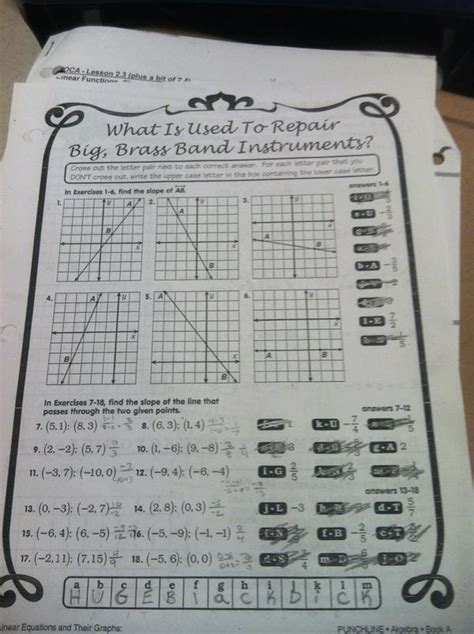
Table of Contents
What's Used to Repair Big Brass Band Instruments? A Comprehensive Guide
Big brass band instruments, like tubas, trombones, and French horns, are complex and often expensive instruments. Understanding how to repair them, or at least knowing what materials and tools are needed, is crucial for both musicians and repair technicians. This comprehensive guide delves into the world of brass instrument repair, exploring the common issues, the materials used, and the techniques employed to restore these magnificent instruments to their former glory.
Common Repairs and the Materials Used
Brass band instrument repairs range from minor adjustments to extensive overhauls. Let's break down some common issues and the materials typically employed in their repair:
1. Dent Repair
Dents are a frequent occurrence, particularly with larger, more susceptible instruments like tubas. Repairing dents often involves specialized tools and techniques.
-
Materials: A variety of tools are used, including dent removers, which can range from simple wooden mallets to more sophisticated pneumatic tools. Brasses and other metals may be used to create makeshift tools and shims. A variety of hammers with varying weights are also vital. Finally, special lubricants can prevent scratching and aid in the repair process.
-
Techniques: Dent removal typically involves carefully manipulating the metal back into its original shape using these tools. The process requires a keen eye, steady hand, and experience to avoid causing further damage.
2. Valve and Piston Repairs
Valve and piston issues are among the most common problems encountered in brass instruments. These issues can range from simple lubrication problems to damaged parts requiring replacement.
-
Materials: Valve oil is essential for proper lubrication. Valve casings, valves, springs, and fells may need to be replaced if damaged. Cork grease is also a vital component for sealing and lubricating valve components.
-
Techniques: Repairing valve problems involves careful disassembly, cleaning, lubrication, and potential replacement of worn or damaged components. Proper alignment and seating of the valves are crucial for optimal performance.
3. Slide Repair (Trombones)
Trombones possess a complex slide mechanism that requires regular maintenance and occasional repair.
-
Materials: Slide grease is crucial for smooth operation. Slide cork might require replacement if worn or damaged. In some cases, slide alignment tools are used to ensure proper function. Fine-grit sandpaper can be used to smooth rough edges.
-
Techniques: Repairing trombone slides often involves cleaning, lubricating, and adjusting the slide to ensure a smooth and airtight seal. Repairing the actual slide components might involve using specialized tools and techniques to straighten bent sections or replace worn parts.
4. Solder Repairs
Leaking solder joints are a common issue in brass instruments. These can be found in various places such as where the bell is soldered to the body, on valves, or other joint sections.
-
Materials: Solder (usually a lead-free alloy appropriate for brass), soldering iron with an appropriate tip, flux, and soldering aid (such as acid flux for better flow and join strength).
-
Techniques: Solder repair demands precision and experience. The area must be thoroughly cleaned before applying flux and soldering the joint. Excessive heat can damage the instrument, requiring a steady hand and experience to control the temperature effectively.
5. Lacquer Repairs
Over time, the lacquer finish on brass instruments can chip, scratch, or wear away.
-
Materials: Lacquer remover, abrasive materials to prepare the surface for new lacquer, lacquer spray, and lacquer thinner. Appropriate protective gear such as a respirator mask is crucial when working with lacquer.
-
Techniques: Repairing lacquer requires careful removal of the damaged lacquer, preparation of the surface, and application of new lacquer. The process requires an understanding of lacquer properties and proper spraying techniques to create a smooth, uniform finish.
Advanced Repairs and Specialized Tools
Some repairs go beyond basic maintenance and require specialized knowledge and tools.
1. Body Repairs:
Serious damage to the instrument's body, such as large dents or cracks, requires advanced techniques.
-
Materials: This might involve specialized metal working tools, brazing materials, and welding equipment. Specialty alloys may be required to match the instrument's original composition.
-
Techniques: These repairs require a high level of expertise and precision. They may necessitate specialist knowledge of metalworking and metallurgy to ensure the structural integrity of the instrument remains intact.
2. Keywork Repairs (French Horns and other instruments with keys):
French horns and some other brass instruments have complex keywork systems that can malfunction.
-
Materials: Key springs, pads, felt, and other intricate components may need to be replaced. Tools for adjusting key alignment are also needed.
-
Techniques: Repairing keywork requires a thorough understanding of the mechanics involved. Precise adjustments and replacements are necessary to ensure proper functioning.
3. Mouthpiece Repairs:
Mouthpieces, whilst not part of the main instrument, can also suffer damage and require repair.
-
Materials: Specific tools for reshaping the mouthpiece rim and abrasives for polishing and smoothing.
-
Techniques: Mouthpiece repair is delicate and specialized, requiring an experienced technician with a high level of precision.
Importance of Professional Repair
While some minor repairs might be attempted by knowledgeable individuals, most complex repairs should be left to experienced instrument repair technicians. Improper repairs can cause further damage, rendering the instrument irreparable or affecting its tone and playability. Professional repair technicians possess the expertise, tools, and materials necessary to perform repairs correctly.
Preventive Maintenance: The Best Repair is Prevention
Regular maintenance is key to preventing significant repairs. This includes:
- Regular cleaning: This prevents build-up of dirt, moisture, and corrosion.
- Proper lubrication: Lubricating valves, slides, and other moving parts ensures smooth operation.
- Careful handling: Avoiding dropping or bumping the instrument minimizes the risk of dents and damage.
- Proper storage: Storing the instrument in a case in a controlled environment prevents damage and corrosion.
By following these preventative measures, you can significantly prolong the life of your brass band instrument and minimize the need for expensive repairs. Remember, a well-maintained instrument is a joy to play, and regular care represents a sound investment for both the musician and the instrument itself.
Latest Posts
Latest Posts
-
If Im 53 What Year Was I Born
Apr 08, 2025
-
How To Say A Little In Spanish
Apr 08, 2025
-
How Many Quarts Are In A 2 Liter Bottle
Apr 08, 2025
-
Distance From Biloxi Mississippi To New Orleans
Apr 08, 2025
-
5am To 12pm Is How Many Hours
Apr 08, 2025
Related Post
Thank you for visiting our website which covers about What Is Used To Repair Big Brass Band Instruments . We hope the information provided has been useful to you. Feel free to contact us if you have any questions or need further assistance. See you next time and don't miss to bookmark.