When Checking For Non Condensables Inside A Recovery Cylinder
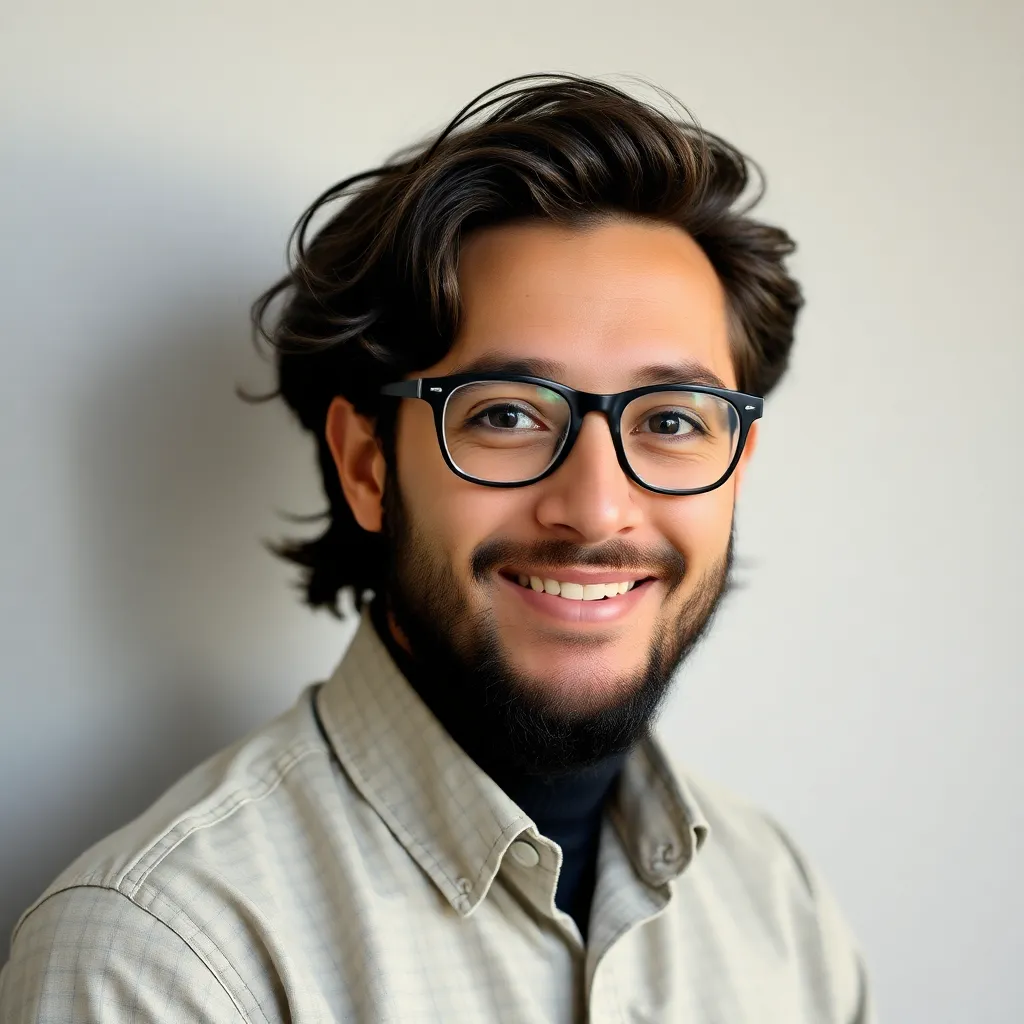
Arias News
May 12, 2025 · 5 min read
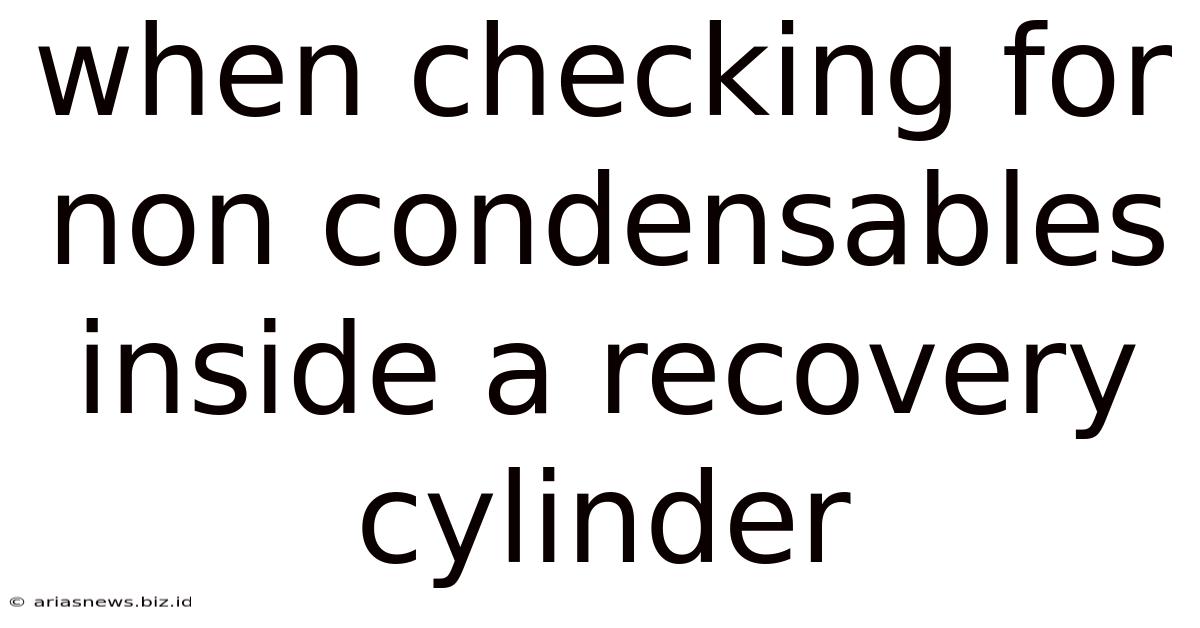
Table of Contents
When Checking for Non-Condensables Inside a Recovery Cylinder
Refrigeration systems rely on the efficient circulation of refrigerant to maintain optimal cooling. The presence of non-condensables, however, significantly hampers this process, leading to reduced efficiency, increased energy consumption, and potential system damage. Understanding how to effectively check for non-condensables within a recovery cylinder is crucial for ensuring the health and longevity of refrigeration equipment. This comprehensive guide delves into the intricacies of this process, offering practical advice and troubleshooting tips for technicians and maintenance professionals.
Understanding Non-Condensables in Refrigeration Systems
Non-condensables are gases that don't condense into a liquid state under the operating pressures and temperatures of a refrigeration system. Unlike the refrigerant, which cycles between liquid and vapor phases, these gases remain in their gaseous form, occupying valuable space within the condenser and hindering the refrigerant's ability to transfer heat efficiently.
Common Non-Condensable Gases:
- Air: The most common contaminant, often introduced during system installation, maintenance, or leaks.
- Nitrogen: Used in leak detection and sometimes inadvertently introduced during servicing.
- Hydrogen: A byproduct of refrigerant breakdown, especially in older systems.
- Carbon Dioxide (CO2): Can enter the system through leaks or decomposition of oil.
The Impact of Non-Condensables:
The presence of even small amounts of non-condensables can have a significant negative impact:
- Reduced Condensing Pressure: Non-condensables occupy space in the condenser, preventing the refrigerant vapor from fully condensing. This leads to a lower condensing pressure, reducing the system's cooling capacity.
- Increased Discharge Temperature: The inability of the refrigerant to fully condense results in higher discharge temperatures from the compressor, potentially leading to overheating and damage.
- Increased Head Pressure: The pressure in the high-side of the system increases, putting extra strain on the compressor and other components.
- Reduced Efficiency: The overall efficiency of the refrigeration system is significantly lowered, leading to increased energy consumption and higher operating costs.
- Compressor Damage: Prolonged operation under these suboptimal conditions can result in compressor failure.
Methods for Detecting Non-Condensables in Recovery Cylinders
Several methods exist for detecting non-condensables in recovery cylinders, each with its own advantages and limitations.
1. Visual Inspection:
While not a definitive test, a visual inspection can provide initial clues. Observe the cylinder for unusual bubbling or frothing during the recovery process. Excessive frothing could indicate the presence of non-condensables. However, this method is not reliable on its own and should be supplemented with more accurate techniques.
2. Pressure Gauge Observation:
Monitoring pressure changes during the recovery and subsequent holding periods can offer insight. If the pressure remains elevated even after the system has been completely evacuated and the cylinder has cooled down, it could suggest the presence of non-condensables. The pressure should stabilize once the refrigerant has fully condensed. A significant pressure discrepancy from expected values warrants further investigation.
3. Temperature Measurement:
Precise temperature readings of the cylinder can help identify non-condensables. A significantly higher temperature than expected for the refrigerant at a given pressure suggests the presence of non-condensables, as they hinder the heat transfer process. Using an accurate thermometer and comparing readings to refrigerant charts is crucial for this method.
4. Liquid Level Observation:
If the recovery cylinder allows for liquid level observation, a significantly lower liquid level than expected, considering the amount of refrigerant recovered, could indicate non-condensables occupying space in the cylinder. However, this method relies on accurate estimation and might not be reliable in all cases.
5. Vacuum Pump and Gauge Method (More Advanced):
This method involves connecting a vacuum pump to the recovery cylinder after the refrigerant has been recovered. Drawing a deep vacuum and observing the pressure gauge can reveal the presence of non-condensables. If the pressure doesn’t reach a near-perfect vacuum after several minutes, it suggests non-condensables are present. This method requires precision equipment and experience in handling vacuum systems.
6. Specialized Non-Condensable Detectors:
Advanced non-condensable detectors specifically designed for refrigerant systems are available. These devices provide accurate readings by measuring the properties of the refrigerant and identifying the presence of gases that don’t match the refrigerant's composition. These detectors are usually expensive but offer the most accurate measurements.
Best Practices for Minimizing Non-Condensables
Preventing the introduction of non-condensables is more efficient than dealing with them after they enter the system. Here are some essential best practices:
- Proper System Evacuation: Always conduct a thorough evacuation of the refrigeration system during installation and maintenance, using a high-capacity vacuum pump for extended periods.
- Cleanliness During Service: Maintain a clean and dust-free environment during all system repairs and maintenance.
- Leak Detection and Repair: Regularly check for leaks and promptly repair any discovered, preventing the ingress of air and other gases.
- Careful Handling of Refrigerant: Use proper handling techniques to minimize contamination during refrigerant charging and recovery.
- Use Quality Equipment: Utilize properly maintained and calibrated tools and equipment to prevent accidental contamination.
Troubleshooting and Addressing Non-Condensables
If non-condensables are detected, the following steps should be taken:
-
Identify the Source: Determine the source of the non-condensables. This may require detailed inspections, leak detection, and analysis of the recovered refrigerant.
-
Separate the Non-Condensables: While not always possible with simple equipment, advanced separation techniques may be employed to remove the non-condensables from the refrigerant. This often requires specialized equipment and expertise.
-
System Purge: A thorough system purge may be necessary to eliminate residual non-condensables. This involves evacuating the system repeatedly to remove trapped gases.
-
Repair Leaks: If leaks are discovered, they must be repaired immediately to prevent further contamination.
-
Refrigerant Recharging: After addressing the non-condensable issue, the system should be recharged with the appropriate refrigerant, following manufacturer’s recommendations.
Conclusion: Prioritizing System Health Through Non-Condensable Management
The presence of non-condensables in refrigeration systems poses a serious threat to efficiency, performance, and longevity. Regular monitoring and proactive measures are vital in minimizing their impact. By employing the detection methods outlined above and adhering to best practices, technicians and maintenance professionals can significantly improve system health and ensure optimal performance of refrigeration equipment. Remember that accurate detection and prompt remediation are key to preventing costly repairs and system failures. The investment in proper equipment and training pays off in the long run through reduced downtime, energy savings, and overall system reliability. Ignoring non-condensables can lead to escalating problems, resulting in more significant and expensive repairs later on. Prioritizing their identification and removal is crucial for maintaining efficient and reliable refrigeration systems.
Latest Posts
Latest Posts
-
What Are All The Factors Of 11
May 12, 2025
-
Which Polygon Has An Interior Angle Sum Of 1080
May 12, 2025
-
Difference Between 100 Meters And 100 Yards
May 12, 2025
-
What Is The Greatest Common Factor Of 60 And 90
May 12, 2025
-
Words Starting With J To Describe Someone
May 12, 2025
Related Post
Thank you for visiting our website which covers about When Checking For Non Condensables Inside A Recovery Cylinder . We hope the information provided has been useful to you. Feel free to contact us if you have any questions or need further assistance. See you next time and don't miss to bookmark.