Which Describes The Cost To Produce One Item
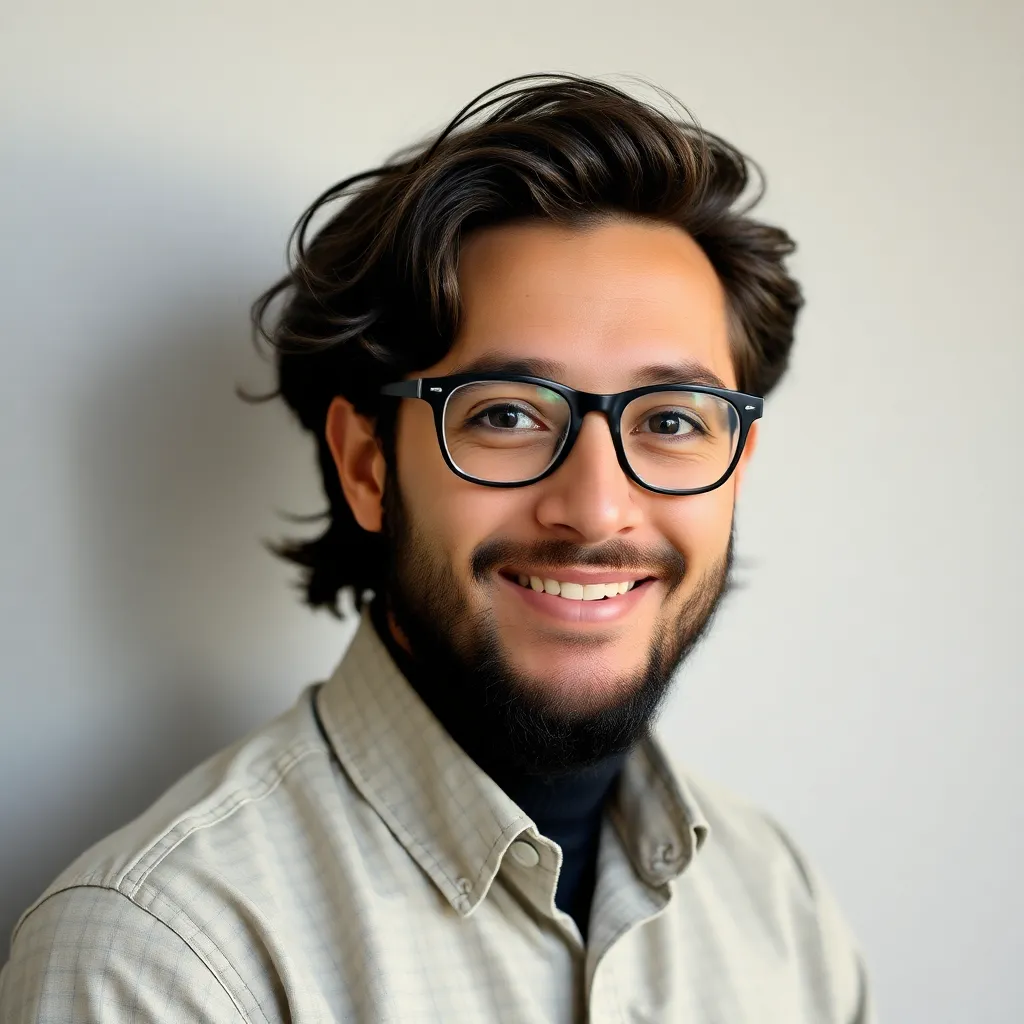
Arias News
May 11, 2025 · 7 min read
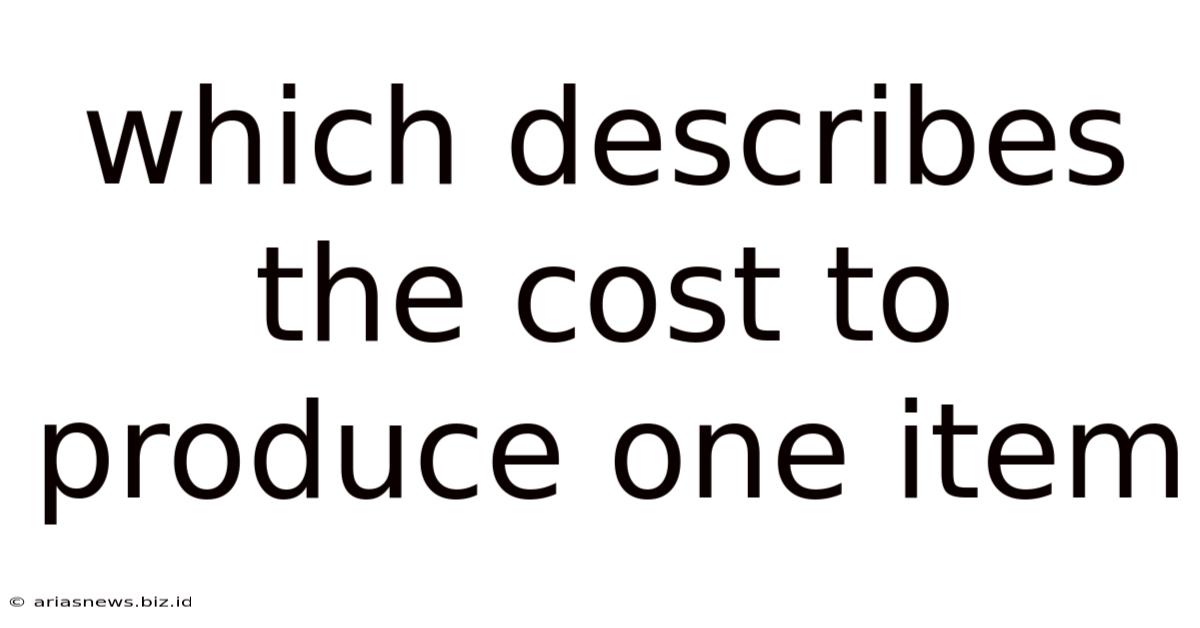
Table of Contents
Decoding the Cost to Produce One Item: A Comprehensive Guide
Understanding the true cost of producing a single item is crucial for businesses of all sizes. It's not simply the price of raw materials; it's a complex calculation encompassing various direct and indirect costs. This comprehensive guide dives deep into the different cost components, providing a clear framework for accurate cost analysis and informed business decisions. Mastering this understanding will empower you to price your products strategically, optimize production processes, and ultimately boost profitability.
The Foundation: Direct Costs
Direct costs are directly attributable to the production of a single item. These are easily traceable and quantifiable, making them relatively straightforward to calculate. Let's break them down:
1. Raw Materials: The Building Blocks
This is the most obvious cost component. Raw materials are the basic ingredients or components needed to manufacture your product. This includes everything from the cotton in a t-shirt to the silicon in a computer chip. Accurate costing requires meticulous tracking of material usage, considering variations in material prices and potential waste. Effective inventory management is key to minimizing waste and maintaining optimal stock levels.
Example: For a bakery producing bread, the raw materials would include flour, yeast, water, salt, and any additional ingredients like sugar or seeds. The cost of each ingredient, multiplied by the quantity used per loaf, constitutes the raw material cost per item.
2. Direct Labor: The Human Element
This encompasses the wages, salaries, and benefits paid to workers directly involved in the production process. This includes the time spent assembling, manufacturing, or otherwise contributing to the creation of the finished product. Accurate tracking of labor hours per unit is critical for precise cost calculation. Time and motion studies can help optimize labor efficiency and reduce direct labor costs.
Example: In the bakery, direct labor includes the wages paid to bakers who knead the dough, shape the loaves, and bake them. The total labor cost is divided by the number of loaves produced to determine the direct labor cost per item.
3. Manufacturing Overhead: Hidden Costs
While not directly tied to a single unit, manufacturing overhead represents the indirect costs necessary for production. These are expenses that support the production process but are difficult to allocate to individual items.
a) Factory Rent and Utilities: The Infrastructure Cost
The cost of renting or owning the manufacturing facility, including utilities like electricity, water, and gas, contributes to the overall production cost. These costs are typically allocated based on factors such as square footage used or energy consumption.
b) Depreciation of Machinery and Equipment: The Wear and Tear
Machinery and equipment depreciate over time. This depreciation cost represents the gradual loss of value of these assets and needs to be factored into the cost per item. This is usually calculated using methods like straight-line depreciation or accelerated depreciation.
c) Factory Supplies and Maintenance: Keeping Things Running
Expenses related to consumable supplies used in the production process (like lubricants, cleaning materials) and the maintenance of machinery and equipment are also included. Regular maintenance is crucial to prevent costly breakdowns and ensure consistent production.
d) Quality Control: Ensuring Standards
The cost of implementing quality control measures, including inspections and testing, is essential for maintaining product quality and reducing waste. This ensures that only finished goods meeting the required standards are shipped out.
Beyond the Direct: Indirect Costs
Indirect costs are more challenging to allocate directly to a single item but are equally crucial for calculating the true cost of production. These costs are often incurred across multiple products and require careful allocation.
1. Administrative Overhead: The Business Backbone
This encompasses the costs associated with managing the business, including salaries of administrative staff, office rent, and utilities. These costs are usually allocated to products based on factors such as revenue or production volume.
2. Selling, General, and Administrative (SG&A) Expenses: Reaching the Market
SG&A costs include expenses related to marketing, sales, distribution, and general administration. These are crucial for bringing the product to market but aren't directly tied to its production. Allocation methods for these costs vary, often based on sales revenue or production volume.
3. Research and Development (R&D): Innovation and Improvement
Investment in R&D is crucial for innovation and improving existing products. While this cost isn't directly tied to a single unit, it's a significant factor impacting the overall long-term cost structure. R&D costs are usually allocated based on a percentage of sales or as a separate line item on the financial statements.
Calculating the Total Cost: Putting It All Together
Once all the direct and indirect costs are identified and calculated, they are summed to arrive at the total cost of production. This total cost is then divided by the number of units produced to determine the cost per item. This provides a crucial baseline for pricing decisions.
Costing Methods: Different Approaches, Same Goal
Various methods are employed for calculating the cost of production, each with its strengths and weaknesses.
1. Absorption Costing: Including All Overhead
This method includes all manufacturing overhead costs in the product cost. It’s widely used for financial reporting purposes but can be less precise for making operational decisions because it doesn't distinguish between fixed and variable overhead.
2. Variable Costing: Focusing on Direct Costs
This method only includes variable manufacturing costs in the product cost. It provides a clearer picture of the cost fluctuations based on production volume but excludes fixed overhead costs. This makes it useful for short-term decision-making but less suitable for long-term financial reporting.
3. Activity-Based Costing (ABC): Detailed Cost Allocation
ABC is a more sophisticated approach that traces costs to specific activities involved in production. It provides a more accurate cost allocation, especially for companies with diverse product lines, as it recognizes the impact of different activities on the overall cost.
Beyond Cost: Pricing Strategies
Understanding the cost per item is the first step in developing a profitable pricing strategy. Several factors influence pricing, including market competition, customer perception, and desired profit margins.
1. Cost-Plus Pricing: Simple and Straightforward
This involves adding a markup percentage to the cost per item to determine the selling price. While simple, it may not account for market dynamics or customer willingness to pay.
2. Value-Based Pricing: Focusing on Customer Perception
This approach emphasizes the perceived value of the product to the customer. Pricing is determined based on the perceived benefits and features, rather than simply the cost of production.
3. Competitive Pricing: Matching Market Rates
This involves setting prices based on the prices charged by competitors. While this ensures market competitiveness, it might not maximize profits if the cost structure differs significantly from competitors.
Optimizing Production Costs: A Continuous Pursuit
Reducing production costs is a constant endeavor for businesses seeking profitability. Several strategies can help optimize costs without compromising quality.
1. Lean Manufacturing: Eliminating Waste
Lean manufacturing principles focus on eliminating waste throughout the production process, from raw materials to finished goods. This reduces costs and enhances efficiency.
2. Process Optimization: Streamlining Operations
Analyzing and streamlining production processes can identify bottlenecks and inefficiencies, resulting in cost savings and increased productivity.
3. Technology Adoption: Automating Processes
Automating repetitive tasks using technology can reduce labor costs, improve accuracy, and enhance efficiency.
4. Supplier Relationship Management: Negotiating Better Deals
Developing strong relationships with suppliers can lead to better pricing and improved supply chain efficiency, reducing raw material costs.
Conclusion: The Ongoing Quest for Cost Efficiency
Determining the cost to produce one item is a multifaceted process requiring a deep understanding of all cost components, both direct and indirect. By utilizing appropriate costing methods, optimizing production processes, and implementing effective pricing strategies, businesses can achieve a competitive edge, enhance profitability, and ensure long-term success. The journey towards cost efficiency is ongoing; continuous monitoring and improvement are essential for sustained growth and resilience in the dynamic business landscape.
Latest Posts
Latest Posts
-
What Is The Square Root Of 71
May 12, 2025
-
How Far Is 50 Miles In Minutes
May 12, 2025
-
How Old Would You Be If Born In 2003
May 12, 2025
-
How Many 1 000 In A Million
May 12, 2025
-
Is Henry A Name In The Bible
May 12, 2025
Related Post
Thank you for visiting our website which covers about Which Describes The Cost To Produce One Item . We hope the information provided has been useful to you. Feel free to contact us if you have any questions or need further assistance. See you next time and don't miss to bookmark.