Is Ductility A Physical Or Chemical Property
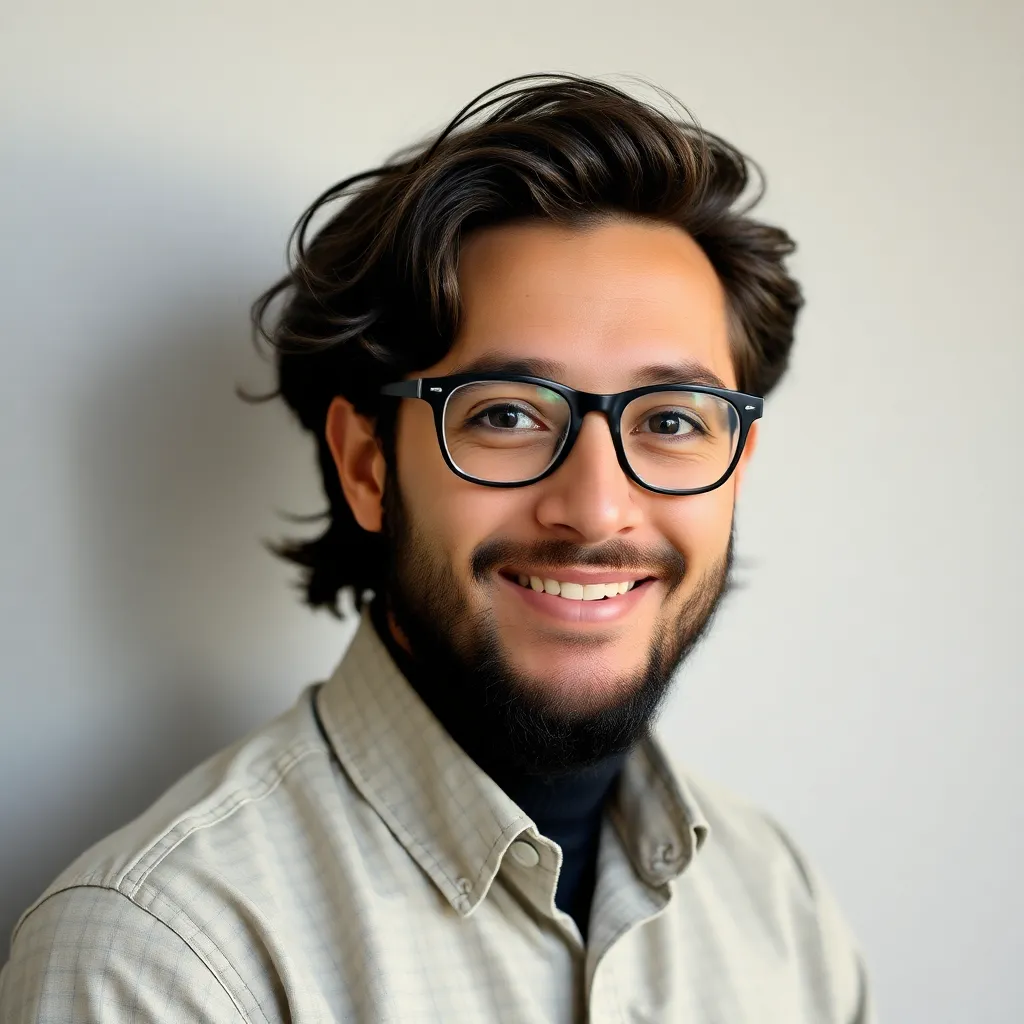
Arias News
Mar 15, 2025 · 6 min read
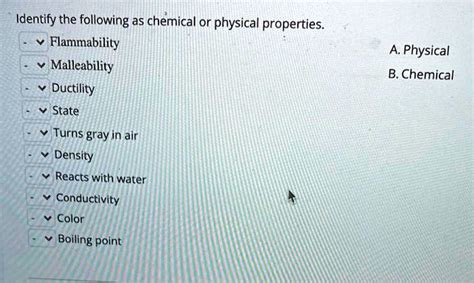
Table of Contents
Is Ductility a Physical or Chemical Property? A Comprehensive Exploration
Ductility, the ability of a material to deform under tensile stress, is a fundamental property extensively studied in materials science and engineering. Understanding whether ductility is a physical or chemical property is crucial for selecting appropriate materials for various applications, from building construction to microelectronics. This comprehensive exploration delves into the nature of ductility, differentiating it from chemical properties and highlighting its importance in material characterization.
Defining Ductility: A Physical Property
Ductility is unequivocally classified as a physical property. Physical properties are characteristics of a substance that can be observed or measured without changing its chemical composition. These properties describe the physical state and behavior of a material, including its appearance, texture, density, and malleability, alongside ductility. Crucially, observing ductility involves stretching or pulling a material; this process does not alter the material's chemical makeup. The material remains the same substance, simply deformed into a new shape.
Distinguishing Ductility from Chemical Properties
Chemical properties, in contrast, describe a substance's ability to undergo a chemical change, transforming into a different substance. Examples include flammability (ability to burn), reactivity with acids, and oxidation (rusting). These properties are only observable through chemical reactions that alter the material's molecular structure. Ductility, on the other hand, involves only a physical change – a change in shape without a change in the material's chemical identity.
Key Difference: The fundamental difference lies in the involvement of chemical bonds. Chemical properties involve the breaking and forming of chemical bonds, altering the substance's molecular structure. Ductility involves the rearrangement of atoms and molecules within the material's structure without breaking or forming chemical bonds. This subtle distinction is crucial in categorizing ductility as a physical property.
Factors Influencing Ductility: Structure and Composition
While ductility is a physical property, its magnitude is significantly influenced by the material's microstructure and chemical composition. This seemingly contradictory statement highlights the interplay between physical and chemical aspects in determining material behavior.
Microstructural Influence: Crystalline Structure and Grain Size
The arrangement of atoms within a material's crystal structure profoundly impacts its ductility. Materials with a face-centered cubic (FCC) structure, like gold and copper, generally exhibit high ductility because their atomic arrangement allows for easy slip and dislocation movement under stress. In contrast, materials with a body-centered cubic (BCC) structure, such as iron at room temperature, tend to be less ductile due to limited slip systems.
Grain size also plays a crucial role. Smaller grains generally lead to improved ductility due to increased grain boundary area, hindering dislocation movement and thus increasing the material's resistance to fracture. Conversely, larger grains allow for easier dislocation motion, potentially resulting in reduced ductility. Techniques like annealing, which control grain size through heat treatment, are often used to tailor a material's ductility.
Compositional Influence: Alloying and Impurities
The presence of alloying elements and impurities significantly impacts a material's ductility. Alloying often enhances a material's mechanical properties, including ductility. For example, adding small amounts of certain elements to steel can improve its ductility, making it more formable. However, excessive alloying or the presence of certain impurities can reduce ductility by hindering dislocation movement or creating brittle phases within the material.
Solid Solution Strengthening: The addition of alloying elements into the crystal lattice of a metal can lead to solid solution strengthening. While this increases strength, it often comes at the cost of reduced ductility. The alloying atoms obstruct dislocation motion, making plastic deformation more difficult.
Second-Phase Particles: The presence of second-phase particles in a material can also affect ductility. These particles can act as obstacles to dislocation movement, leading to decreased ductility but increased strength. The size, distribution, and type of second-phase particles all influence their impact on ductility.
Measuring Ductility: Practical Tests and Applications
Ductility is quantitatively measured through various mechanical testing methods. These tests provide critical information for material selection and design.
Tensile Testing: A Standard Measurement
Tensile testing is the most common method for assessing ductility. In this test, a standardized specimen is subjected to a uniaxial tensile load until fracture. Ductility is then expressed as either percent elongation or reduction in area.
- Percent elongation: This represents the percentage increase in the specimen's length before fracture. A higher percentage elongation indicates greater ductility.
- Reduction in area: This represents the percentage decrease in the specimen's cross-sectional area at the point of fracture. Similar to percent elongation, a higher reduction in area implies greater ductility.
Other Ductility Tests
Other techniques, such as bend tests and impact tests, provide additional insights into a material's ductility. Bend tests assess a material's ability to deform under bending stress, while impact tests evaluate its resistance to fracture under sudden impact loading. These tests can be particularly useful for evaluating the ductility of materials at different temperatures or under various loading conditions.
Applications of Ductility: Shaping Materials for Diverse Uses
The ductility of a material directly impacts its suitability for various applications. Many manufacturing processes rely on a material's ability to deform plastically without fracturing.
Metal Forming: Shaping Metals into Desired Forms
Ductile materials are essential in metal forming processes such as rolling, drawing, forging, and extrusion. These processes rely on the material's ability to undergo significant plastic deformation without breaking. High ductility ensures that the metal can be shaped into complex forms with minimal defects. Examples include the production of wires (drawing), sheets (rolling), and intricate components (forging).
Wire Drawing and Sheet Metal Forming: Precision and Flexibility
Wire drawing is a process where a metal rod is pulled through a series of dies to reduce its diameter. The ductility of the metal is crucial for preventing fracture during this process. Similarly, sheet metal forming relies heavily on the ductility of the sheet material to allow for bending, stamping, and other shaping operations.
Welding and Joining: Ductility's Role in Material Integrity
Ductility plays a crucial role in the weldability of metals. A ductile metal can deform around the weld zone, accommodating stresses and preventing cracks from forming. This property is essential for maintaining the structural integrity of welded joints.
Conclusion: Ductility as a Critical Physical Property
In conclusion, ductility is definitively a physical property. It describes the ability of a material to deform under tensile stress without fracturing, a characteristic observable without changing the material's chemical composition. While its magnitude is influenced by microstructural features and chemical composition, the process of observing ductility itself does not involve a chemical change. Understanding and quantifying ductility is essential in materials science and engineering, guiding material selection for various applications where the ability to deform plastically is crucial. From shaping metals into complex forms to ensuring the structural integrity of welded joints, ductility remains a cornerstone property for numerous engineering applications. Further research continues to explore the intricate relationships between microstructural features, chemical composition, and the resulting ductility, leading to advancements in material design and processing.
Latest Posts
Latest Posts
-
How Many Cups Is 12 Oz Of Broccoli Florets
Mar 15, 2025
-
How To Pass Stage 9 On Bloxorz
Mar 15, 2025
-
Least Common Multiple Of 4 And 12
Mar 15, 2025
-
Can You Get Your Hair Wet After A Perm
Mar 15, 2025
-
Why Did Little Joe Always Wear Gloves On Bonanza
Mar 15, 2025
Related Post
Thank you for visiting our website which covers about Is Ductility A Physical Or Chemical Property . We hope the information provided has been useful to you. Feel free to contact us if you have any questions or need further assistance. See you next time and don't miss to bookmark.